Home » Blog » Variable frequency drive » Can an induction motor give out full torque with a VFD?
Can an induction motor give out full torque with a VFD?
A good motor with a good variable frequency drive can give 100% of nominal torque at 5% of rated speed, and sometimes at such speed torque should be also higher. If possible, take care to increase cooling not only by convection in air, but also by conduction to cool metal base or metal flange. You can also increase infrared emission using a treated motor surface to increase heat emission (Alumite finishing, or some black paints or treatments). You can also improve the bearing efficiency - if loaded - using some super-lubricants (i.e.: Prolong grease) to reduce friction and related heat generation.
Many of the new motors have a ratio in their data sheets called a turn down ratio which is the ratio between full speed and low speed at full torque. Typical ones are 10:1 at constant torque. If your motor is operating within the turn down ratio all is well. With the presence of the fan you can go even lower provided that the motor manufacture agrees.
The easier one is you will need to overcome the increasing influence of winding resistance (which changes with temperature, of course, as well as with rotor resistance) as the reactance decreases with frequency by a non-linear V/Hz control coming from the FOC algorithm. You may want to consider including an advanced observer or model reference adaptive control scheme to maintain high performance control. The more difficult problem is at slow speeds the rotor heat transfer mechanism is much different than at high speeds due to lack of convective airflow in and around the rotor surfaces. If you are using your independent cooling to move air over the outside of the machine, the rotor will likely overheat at slow speed, full torque. You will have to provide active cooling for the rotor.
Many of the new motors have a ratio in their data sheets called a turn down ratio which is the ratio between full speed and low speed at full torque. Typical ones are 10:1 at constant torque. If your motor is operating within the turn down ratio all is well. With the presence of the fan you can go even lower provided that the motor manufacture agrees.
The easier one is you will need to overcome the increasing influence of winding resistance (which changes with temperature, of course, as well as with rotor resistance) as the reactance decreases with frequency by a non-linear V/Hz control coming from the FOC algorithm. You may want to consider including an advanced observer or model reference adaptive control scheme to maintain high performance control. The more difficult problem is at slow speeds the rotor heat transfer mechanism is much different than at high speeds due to lack of convective airflow in and around the rotor surfaces. If you are using your independent cooling to move air over the outside of the machine, the rotor will likely overheat at slow speed, full torque. You will have to provide active cooling for the rotor.
You may also like:
On electric drive large NG compressors, inlet pressure 70 psi, outlet about 1100 constant torque, what about electrical load, especially the reactive component, is it dynamic or relatively static?
If it is a ...
Someone wants to upgrade his tomato packing plant so he installs VFDs on the motors that have been in service since 1963 when they were first installed. Run them on the new variable frequency drives and they ...
Before only servo drive used to run by feedback given by motor but now a days we can also use variable speed drive while taking feedback from motor both is used for control position, velocity and save power, ...
Most of the "bad press" for magnetic wedges comes from rewind shops, actually. Either the incorrect material is used (ranging from a poor magnetic profile to one that is not magnetic at all), or a bad match ...
but the inverters must have a common controller. In other words both inverters are controlled by a single system. That isn't specifically 2 separate variable frequency drives on one motor. but similar. ...
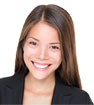
Hot Tags
Featured
7 months back I was involved in a harmonics evaluation study at Budweiser. This was one of many I've participated in over the past 20 years, basically because in facilities like ...
Most of variable speed drives are applying on high temperature fans, kiln head coal mill fans, kiln head surplus fans, raw mill circulating fans and so on. Two production lines ...
Variable speed drive application in purification system optimizes the system performance, improves purification effect, reduces power consumption greatly. According to related ...
The motor power factor does not make a big difference other than giving an idea of loading. In regards to the variable speed drive fixing power factor everyone is mostly correct. ...
A soft starter is a basic device which will ramp up the speed of your motor to full speed over a preset time, easing mechanical stress and also easing the high inrush currents ...
What's New
Variable Speed Drive Harmonics
Variable speed drive energy saving in cement industry
PLC and DAQ
Is it good to do preventive maintenance for variable speed drives
Does motor starts number affect motor life?
Variable speed drive for ID Fans in mining industry
Regenerative power frequency back to line power
Variable speed drive for axial-flow fans
Variable speed drive energy saving in cement industry
PLC and DAQ
Is it good to do preventive maintenance for variable speed drives
Does motor starts number affect motor life?
Variable speed drive for ID Fans in mining industry
Regenerative power frequency back to line power
Variable speed drive for axial-flow fans