7 months back I was involved in a harmonics evaluation study at Budweiser. This was one of many I've participated in over the past 20 years, basically because in facilities like this not one or two, but hundreds of variable speed drives (VSD) are in use. They are but one of many plants using variable speed drives for nearly all of their production controls. Capacitive reactance is inescapable when capacitors are in use in a circuit, as is inductive reactance when motors are operating, or any other component incorporating electro-magnetic coils. This reactance is the issue when dealing with harmonics, as can be the power supply to the facility itself. All variable speed drives employ capacitors.
A more efficient variable speed drive for motors could help the ubiquitous, energy-sucking devices make another leap in energy efficiency. The problem is that most motors are oversized because of high torque requirements that are only needed for a small portion of the motor’s use.
Before only servo drive used to run by feedback given by motor but now a days we can also use variable speed drive while taking feedback from motor both is used for control position, velocity and save power, but servo drive we used to control by plc according to what we write the program but variable speed drive used to control by plc program written in it and we can't modified more vsd plc program but we can make any program for servo drive while using plc.
We all know that a cable is sized by:
1.- Current carrying capacity (with all installation adjusting factors)
2.- Voltage drop
3.- Starting voltage drop (in case of motors)
4.- Short circuit
1.- Current carrying capacity (with all installation adjusting factors)
2.- Voltage drop
3.- Starting voltage drop (in case of motors)
4.- Short circuit
Theoretically a system that is based VSD should have the right to be named servo system just when it has a feedback system that is connected to the load. I've read a lot of comments were the word servo is associate to high performance. I have to say that on a lot of industrial drives, the micros that are handling the closing of the current and speed or position loops, are nicer in drives that are typically sold/specialized for PM motors.
It is possible to power a three phase motor from a single phase power supply and using a capacitor bank to create the rotating magnetic field. Basically the capacitor banks ensures that there is a phase difference between the current and the voltage.
Converting a synchronous motor to an induction motor is easily done, to most motors, by shorting the rings, however, you would most likely need to use a properly sized VFD to get the starting torque you need. If you are interested to do such an upgrade you should consider the age of the motor and any other peripherals (gearbox, etc.) in the drive train.
1. Slip energy recovery with the current motor but with dual inverter on rotor side, which may not be too expensive as it is lower power on rotor side and no change in motor.
2. Slip ring motor with shorted slip ring and stator side inverter control, which may be expensive due to higher cost of electronics for the higher power rating of stator side.
3. Sq cage motor with stator side inverter control, which may be expensive because of motor replacement and higher cost of electronics for the higher power rating of stator side.
2. Slip ring motor with shorted slip ring and stator side inverter control, which may be expensive due to higher cost of electronics for the higher power rating of stator side.
3. Sq cage motor with stator side inverter control, which may be expensive because of motor replacement and higher cost of electronics for the higher power rating of stator side.
Another cause assuming reduced voltage start, star/delta, autotransformer, primary resistance, soft start etc., could be that the motor is not delivering torque sufficient to accelerate the connected load to speed. That is the starting current and starting time under RVS conditions exceeds that permissible by the overload curve. A more advanced protection strategy such as motor thermal modeling may be required. Motor thermal modeling allows the user to 'match' the curves of the protection device to the connected motor.
Actually, AC motor can be also applied with the used of AC Drive, Frequency Inverter. However, based on my actual encountered of almost different type of motors, from fractional size to medium voltage size, from various Manufacturing Industries particularly in Cement Plant, you have to oversize the AC Motor to match the torque carried by the DC Motor.
When select the CT ratio of 50/1 A for 6.6 kV drives where the SC rating of system is 40 kA, 50 protection may not operate because of CT saturation. Again, if the CT is not saturated, the relay terminal may not withstand the current >100 A (for 1 A sec). In case of 50/1 CT, for a fault current of 40 kA, the CT secondary will be having a current of 800A.
As far as running two cables for reliability, the problem is that the failure of one parallel set of conductors reduces the available current to the motor, preventing it from starting. If you are seeking parallel redundancy, each triplex or set of three phases of conductors needs to be sized to carry the full load.
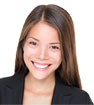
Hot Tags
Featured
7 months back I was involved in a harmonics evaluation study at Budweiser. This was one of many I've participated in over the past 20 years, basically because in facilities like ...
Most of variable speed drives are applying on high temperature fans, kiln head coal mill fans, kiln head surplus fans, raw mill circulating fans and so on. Two production lines ...
Variable speed drive application in purification system optimizes the system performance, improves purification effect, reduces power consumption greatly. According to related ...
The motor power factor does not make a big difference other than giving an idea of loading. In regards to the variable speed drive fixing power factor everyone is mostly correct. ...
A soft starter is a basic device which will ramp up the speed of your motor to full speed over a preset time, easing mechanical stress and also easing the high inrush currents ...
What's New
Variable Speed Drive Harmonics
Variable speed drive energy saving in cement industry
PLC and DAQ
Is it good to do preventive maintenance for variable speed drives
Does motor starts number affect motor life?
Variable speed drive for ID Fans in mining industry
Regenerative power frequency back to line power
Variable speed drive for axial-flow fans
Variable speed drive energy saving in cement industry
PLC and DAQ
Is it good to do preventive maintenance for variable speed drives
Does motor starts number affect motor life?
Variable speed drive for ID Fans in mining industry
Regenerative power frequency back to line power
Variable speed drive for axial-flow fans