Home » Blog » Motor control » Derating motor capacity base on altitude
Derating motor capacity base on altitude
Altitude Standard motors are designed to operate below 3300 feet. Air is thinner and heat is not dissipated as quickly above 3300 feet. Most motors must be derated for altitude. The following chart gives typical horsepower derating factors, but the derating factor should be checked for each motor. A 50 HP motor operated at 6000 feet, for example, would be derated to 47 HP, providing the 40°C ambient rating is still required.
Altitude Deratring factor
3300-5000 0.97
5001-6600 0.94
6601-8300 0.90
8301-9900 0.86
9901-11500 0.82
50HP * 0.94 = 47HP
Power and heat dissipation is one problem. But there is a completely different issue of voltage breakdown. Even with running at no load there is a danger of voltage flashover (arc) if the machine is used above its rated altitude.
Some definition of the required distances are given in IEC 61010. However, a device designed for lower altitude might not be usable at all at much higher altitude - and no amount of derating will fix that. This is simply linked to the physical spacing between the conductors. The only case where this does not apply is if the conductors are completely enclosed in insulation (e.g. potted in resin or immersed in oil).
However, in the IEC 61010 the same dimension requirements are given up to 2000 m, so not sure what this means. Ideally one should ask the original manufacturer/designer.
Altitude Deratring factor
3300-5000 0.97
5001-6600 0.94
6601-8300 0.90
8301-9900 0.86
9901-11500 0.82
50HP * 0.94 = 47HP
Power and heat dissipation is one problem. But there is a completely different issue of voltage breakdown. Even with running at no load there is a danger of voltage flashover (arc) if the machine is used above its rated altitude.
Some definition of the required distances are given in IEC 61010. However, a device designed for lower altitude might not be usable at all at much higher altitude - and no amount of derating will fix that. This is simply linked to the physical spacing between the conductors. The only case where this does not apply is if the conductors are completely enclosed in insulation (e.g. potted in resin or immersed in oil).
However, in the IEC 61010 the same dimension requirements are given up to 2000 m, so not sure what this means. Ideally one should ask the original manufacturer/designer.
You may also like:
SV-PWM is actually just a modulation algorithm which translates phase voltage (phase to neutral) references, coming from the controller, into modulation times/duty-cycles to be applied to the PWM ...
Clean the variable frequency drive heatsink and check or replace the fans. I like new fans every five years. I also double check the drives installation. This is a good opportunity to make corrections to the ...
It involves my proprietary power electronics, DC machines working in concert with AC grids, bi-directionally blocking the traditional amp draws of the AC grid and bi-directionally permitting forward emf ...
1a. if the driver is a synchronous motor there isn't a power factor problem as the motor will be either 1.0 or leading PF
1b. if the driver is induction: check with the motor manufacturer for the power ...
The good of PLC is it work in a hazard environment and robust. We have
Omron CQM1 for DI water plant, after a big flooding in Thailand ( stay
under water for more than 2 months) after we clean dry and bake ...
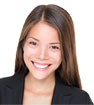
Hot Tags
Featured
7 months back I was involved in a harmonics evaluation study at Budweiser. This was one of many I've participated in over the past 20 years, basically because in facilities like ...
Most of variable speed drives are applying on high temperature fans, kiln head coal mill fans, kiln head surplus fans, raw mill circulating fans and so on. Two production lines ...
Variable speed drive application in purification system optimizes the system performance, improves purification effect, reduces power consumption greatly. According to related ...
The motor power factor does not make a big difference other than giving an idea of loading. In regards to the variable speed drive fixing power factor everyone is mostly correct. ...
A soft starter is a basic device which will ramp up the speed of your motor to full speed over a preset time, easing mechanical stress and also easing the high inrush currents ...
What's New
Variable Speed Drive Harmonics
Variable speed drive energy saving in cement industry
PLC and DAQ
Is it good to do preventive maintenance for variable speed drives
Does motor starts number affect motor life?
Variable speed drive for ID Fans in mining industry
Regenerative power frequency back to line power
Variable speed drive for axial-flow fans
Variable speed drive energy saving in cement industry
PLC and DAQ
Is it good to do preventive maintenance for variable speed drives
Does motor starts number affect motor life?
Variable speed drive for ID Fans in mining industry
Regenerative power frequency back to line power
Variable speed drive for axial-flow fans