Home » Blog » Motor control » Electric motor applications noise
Electric motor applications noise
I have been involved with the manufacturing and application of low (460 V), medium (4 kV) and high (13 kV) motors and am now on the driven equipment side of the coupling (large compressors), and the writing of IEEE and API equipment standards.
Many large end users endeavor to meet local or national noise exposure codes. And lots of the code setters are working to reduce noise exposure, with varying success.
In one experience (decades ago) in a California location, I was concerned about the 3000 Hp 3600 rpm motor driving a water pump, and meeting 85 dBA on my motor. As it turned out, the large motor was fine. The problem child turned out to be a 5 Hp motor driving a gear pump on the lube oil console (provided by the water pump vendor). It was noisier than my big unit.
Just think what a centrifugal compressor running at 10,000 rpm sounds like.
Typically, unmodified rotors spinning at higher speeds (ie 3600 rpm) have high noise at high frequencies (the most irritating part of dB A scale). 4 Pole, somewhat less, and so forth. Changing fans, baffels, etc. and etc. can help. Paddle wheel type fans are noisy, but bi-directional. Curved blade fans are quieter, but have to be uni-directional. Beyond that could be frame modification, part re-design (for weight, mass, harmonic performance.....)
In more situations, noise engineers are being employed to analyze noisy environments to engineer noise abatement beyond what the machine manufacturer can do. Building design changes, noise barriers, etc. (very expensive). For them, overall values (dBA) aren't good enough: they need not only octave band levels, but measurements taken at a wide range of locations spread throughout the installed environment (to the side(s), top, behind, etc.) for each piece of equipment. Models and computer constructs are nice, but the proof is in the actual installation and testing with microphones. It is the opposite of tuning a concert hall to get noise improvement: this is de-tuning to get noise reduction (and self-cancellation).
In the end, it comes down to money.
If a guarantee is involved with stiff liquidated damages, then lots of testing and certification on each serial numbered unit is likely to be necessary. (not to mention the cost of law suits....). Like the supply of a nuclear reactor: the reactor is free, it is the paper work that costs billions.
If extrapolation of values from typical machines using a quickie hand held meter is ok, then the impact is minimal.
Many large end users endeavor to meet local or national noise exposure codes. And lots of the code setters are working to reduce noise exposure, with varying success.
In one experience (decades ago) in a California location, I was concerned about the 3000 Hp 3600 rpm motor driving a water pump, and meeting 85 dBA on my motor. As it turned out, the large motor was fine. The problem child turned out to be a 5 Hp motor driving a gear pump on the lube oil console (provided by the water pump vendor). It was noisier than my big unit.
Just think what a centrifugal compressor running at 10,000 rpm sounds like.
Typically, unmodified rotors spinning at higher speeds (ie 3600 rpm) have high noise at high frequencies (the most irritating part of dB A scale). 4 Pole, somewhat less, and so forth. Changing fans, baffels, etc. and etc. can help. Paddle wheel type fans are noisy, but bi-directional. Curved blade fans are quieter, but have to be uni-directional. Beyond that could be frame modification, part re-design (for weight, mass, harmonic performance.....)
In more situations, noise engineers are being employed to analyze noisy environments to engineer noise abatement beyond what the machine manufacturer can do. Building design changes, noise barriers, etc. (very expensive). For them, overall values (dBA) aren't good enough: they need not only octave band levels, but measurements taken at a wide range of locations spread throughout the installed environment (to the side(s), top, behind, etc.) for each piece of equipment. Models and computer constructs are nice, but the proof is in the actual installation and testing with microphones. It is the opposite of tuning a concert hall to get noise improvement: this is de-tuning to get noise reduction (and self-cancellation).
In the end, it comes down to money.
If a guarantee is involved with stiff liquidated damages, then lots of testing and certification on each serial numbered unit is likely to be necessary. (not to mention the cost of law suits....). Like the supply of a nuclear reactor: the reactor is free, it is the paper work that costs billions.
If extrapolation of values from typical machines using a quickie hand held meter is ok, then the impact is minimal.
You may also like:
1. Slip energy recovery with the current motor but with dual inverter on rotor side, which may not be too expensive as it is lower power on rotor side and no change in motor.
2. Slip ring motor with shorted ...
Converting a synchronous motor to an induction motor is easily done, to most motors, by shorting the rings, however, you would most likely need to use a properly sized VFD to get the starting torque you need. ...
Due to current decrement in the Generator during fault conditions the Back-up protection with IDMT relay for a generator in the Electrical protection Scheme becomes complicated. Accordingly, the setting of the ...
The motor power factor does not make a big difference other than giving an idea of loading. In regards to the variable speed drive fixing power factor everyone is mostly correct. A variable speed drive will ...
Explaining some premature motor winding failures (multiple manufacturers) on VFD (multiple manufacturers) driven motors in high elevations. Some motors are VPI, all are inverter rated. Voltage varies from ...
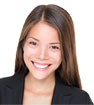
Hot Tags
Featured
7 months back I was involved in a harmonics evaluation study at Budweiser. This was one of many I've participated in over the past 20 years, basically because in facilities like ...
Most of variable speed drives are applying on high temperature fans, kiln head coal mill fans, kiln head surplus fans, raw mill circulating fans and so on. Two production lines ...
Variable speed drive application in purification system optimizes the system performance, improves purification effect, reduces power consumption greatly. According to related ...
The motor power factor does not make a big difference other than giving an idea of loading. In regards to the variable speed drive fixing power factor everyone is mostly correct. ...
A soft starter is a basic device which will ramp up the speed of your motor to full speed over a preset time, easing mechanical stress and also easing the high inrush currents ...
What's New
Variable Speed Drive Harmonics
Variable speed drive energy saving in cement industry
PLC and DAQ
Is it good to do preventive maintenance for variable speed drives
Does motor starts number affect motor life?
Variable speed drive for ID Fans in mining industry
Regenerative power frequency back to line power
Variable speed drive for axial-flow fans
Variable speed drive energy saving in cement industry
PLC and DAQ
Is it good to do preventive maintenance for variable speed drives
Does motor starts number affect motor life?
Variable speed drive for ID Fans in mining industry
Regenerative power frequency back to line power
Variable speed drive for axial-flow fans