Home » Blog » Motor control » Motor bearing failures with VFD
Motor bearing failures with VFD
Common mode currents are motor bearing killers. 1) use as low a carrier frequency as the VFD will allow. 2) make sure that one bearing is grounded and the other is insulated 3) use a dv/dt filter 4) make sure that the bearings installed are proper for the load, roller or ball bearings 5) Use an Aegis or Hedwig shaft grounding device.
We have recently changed the lubricating grease for these machines and had discussions with the machinery manufacturer regarding grease type, quantity and interval to make sure we are maintaining everything correctly. The first failure we experienced saw the bearing balls "eroded" away to look like pebbles on a beach. The second failure on the same motor was a seized bearing on the DE (motor is directly coupled to a compressor air-end with a flexible rubber insert). This unit was an 80kw motor which since we replaced the motor has run for two years without any problems. (The customer insisted on a new motor after the second failure took place only 4 weeks after the first repair). Our re-winder told us there was no need for insulated bearings as the motor end cap and retaining bolt holes were already insulated. I am still skeptical about that. Unfortunately I haven’t been able to find the bearings we removed from the failed unit to have them examined. We have had a similar problem on a 37kw and a 55kw version.
Unfortunately the smaller one cannot be greased as it uses "sealed for life" bearings. We are now scheduling in the re-bearing of this motor at about 6000 hour intervals so as to prevent an out-of-warranty failure. The lead length from the inverter is quite short on all units - max 2 meters. The frequency range varies depending on the kw rating of the machine - motor rpm is approx 1500-7000, once again depending on kw rating.
These failures usually will occur faster in a high torque situation at low to medium speeds like an extruder.
Also, if you are using a gearbox directly coupled to the motor, take the same precautions with it. Common mode can be transferred through it and cause similar issues.
Concerns others have raised about lubricants are valid. Make sure the lube is NON conductive.
On these large horsepower motors typical design for variable frequency drive power would be to insulate ODE, opposite drive end bearing and provide a shaft current device to mitigate any bearing currents (Aegis). Also maintain per the motor manufactures guidelines amount and frequency of greasing, dependent on temperature, running hours, atmospheric conditions/application. The recommended grease for electric motors has been Siemens, Reliance for a number of years as typical industrial applications.
The other thing not mentioned is lead lengths and switching frequency. It is not uncommon with various manufactures and drive designs to see common mode noise which will become an issue quickly with lead lengths in excess of 100 feet. There are numerous ways to help reduce this using reactors on the drive output, reducing switching frequency, dv/dt filters, etc.
We have recently changed the lubricating grease for these machines and had discussions with the machinery manufacturer regarding grease type, quantity and interval to make sure we are maintaining everything correctly. The first failure we experienced saw the bearing balls "eroded" away to look like pebbles on a beach. The second failure on the same motor was a seized bearing on the DE (motor is directly coupled to a compressor air-end with a flexible rubber insert). This unit was an 80kw motor which since we replaced the motor has run for two years without any problems. (The customer insisted on a new motor after the second failure took place only 4 weeks after the first repair). Our re-winder told us there was no need for insulated bearings as the motor end cap and retaining bolt holes were already insulated. I am still skeptical about that. Unfortunately I haven’t been able to find the bearings we removed from the failed unit to have them examined. We have had a similar problem on a 37kw and a 55kw version.
Unfortunately the smaller one cannot be greased as it uses "sealed for life" bearings. We are now scheduling in the re-bearing of this motor at about 6000 hour intervals so as to prevent an out-of-warranty failure. The lead length from the inverter is quite short on all units - max 2 meters. The frequency range varies depending on the kw rating of the machine - motor rpm is approx 1500-7000, once again depending on kw rating.
These failures usually will occur faster in a high torque situation at low to medium speeds like an extruder.
Also, if you are using a gearbox directly coupled to the motor, take the same precautions with it. Common mode can be transferred through it and cause similar issues.
Concerns others have raised about lubricants are valid. Make sure the lube is NON conductive.
On these large horsepower motors typical design for variable frequency drive power would be to insulate ODE, opposite drive end bearing and provide a shaft current device to mitigate any bearing currents (Aegis). Also maintain per the motor manufactures guidelines amount and frequency of greasing, dependent on temperature, running hours, atmospheric conditions/application. The recommended grease for electric motors has been Siemens, Reliance for a number of years as typical industrial applications.
The other thing not mentioned is lead lengths and switching frequency. It is not uncommon with various manufactures and drive designs to see common mode noise which will become an issue quickly with lead lengths in excess of 100 feet. There are numerous ways to help reduce this using reactors on the drive output, reducing switching frequency, dv/dt filters, etc.
You may also like:
What about the frequency of the small amount of the power which back to the network its depend on the speed of the rotor and number of poles f=60/N.P? In another word assume I have AC generator give AC power ...
In electronic design, they use "time simulation" (or "dynamic simulation"), which is an off-line calculation of how a system might respond to various inputs. The inputs are mathematical in this case, and the ...
Therefore, such operation methods not only meet the heating requirements, improve operational efficiency, but also save lots of electricity energies. However, in those operation methods, it requires the ...
Contact the local variable frequency drive distributors and see if there are any classes on VFDs you can attend. These are periodically given by there various manufacturers to promote the use of their brand. ...
DC Motor now a days mostly used for precise speed control of Motor Application,in order to replace the DC motor with AC Induction Motor keep in mind that the initial Torque of the Motor of Load to be Calculate ...
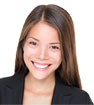
Hot Tags
Featured
7 months back I was involved in a harmonics evaluation study at Budweiser. This was one of many I've participated in over the past 20 years, basically because in facilities like ...
Most of variable speed drives are applying on high temperature fans, kiln head coal mill fans, kiln head surplus fans, raw mill circulating fans and so on. Two production lines ...
Variable speed drive application in purification system optimizes the system performance, improves purification effect, reduces power consumption greatly. According to related ...
The motor power factor does not make a big difference other than giving an idea of loading. In regards to the variable speed drive fixing power factor everyone is mostly correct. ...
A soft starter is a basic device which will ramp up the speed of your motor to full speed over a preset time, easing mechanical stress and also easing the high inrush currents ...
What's New
Variable Speed Drive Harmonics
Variable speed drive energy saving in cement industry
PLC and DAQ
Is it good to do preventive maintenance for variable speed drives
Does motor starts number affect motor life?
Variable speed drive for ID Fans in mining industry
Regenerative power frequency back to line power
Variable speed drive for axial-flow fans
Variable speed drive energy saving in cement industry
PLC and DAQ
Is it good to do preventive maintenance for variable speed drives
Does motor starts number affect motor life?
Variable speed drive for ID Fans in mining industry
Regenerative power frequency back to line power
Variable speed drive for axial-flow fans